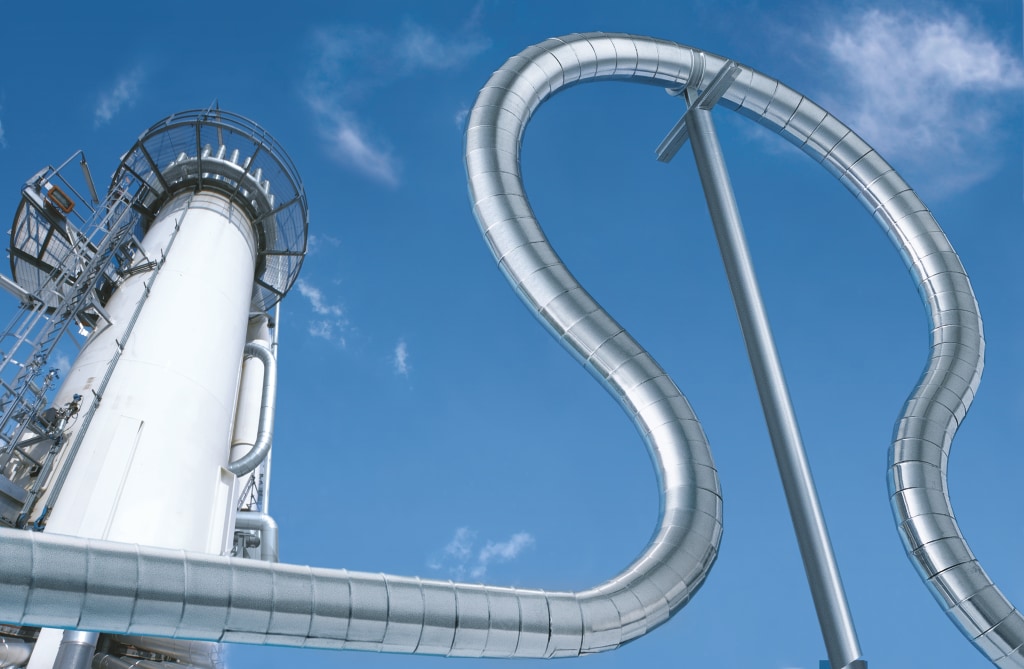
Vital role of gases in petrochemical processing and refining
In petrochemical processing and refining, industrial gases perform a number of key tasks, often serving as invisible helpers and problem-solvers. They are used not only as petrochemical feedstocks, but also as reactants and oxidative agents. In addition, they support hydrotreating, process intensification, process and quality control, inerting, storage and transport.
Gases role from development to implementation
We offer a wide range of gas-related solutions spanning state-of-the-art application technologies, end-to-end hardware supply schemes, development tools such as experimental set-ups, calculation programs for process design and software to support safety competence, for instance. Our experts work closely with you in order to develop and optimise the gas application solution best suited to your needs. In addition, we support all stages of the project lifecycle, from trails and design through to implementation and start-up.
Would like to learn more about Petrochemical processing and refining
Not only legislation but more extensive processing of residues and higher diesel demand compared with petrol will also increase hydrogen's demand.
There are various hydrotreating processes in a refinery. To name a few:
● Hydrodesulphurisation: sulphur compounds are hydrogenated to hydrogen sulphide H2S as feed for Claus
plants
● Hydroisomerisation: normal paraffins are converted into iso-paraffins to improve the product
properties (e.g. RON)
● Dearomatisation: aromatics are hydrogenated to cyclo paraffins or alkanes
● Hydrocracking: long-chain hydrocarbons are cracked to shorter chains in the gasoline range.
Main processes for hydrogen production:
● Steam reforming of methane or other hydrocarbons
● Gasification of organic feedstock to syngas (H2/CO)
● Recovery from gaseous waste streams
● Electrolysis of NaC
Process consulting, financing, erection and start-up are all services offered by Linde. We can also provide
hydrogen plant operation (over-the-fence-supply), maintenance and repair and emergency supply arrangement to
ensure that your business is working at its optimum.
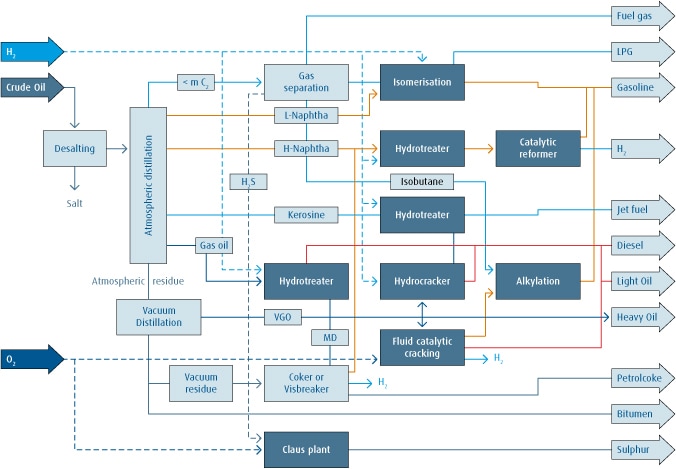
Hover on the image to enlarge it
Claus plants in refineries process concentrated hydrogen sulphide (H2S) fractions converting them into
elemental sulphur. They can also remove pollutants, particularly by decomposing ammonia.
Stricter environmental regulation leads to products with lower sulphur content. As a result Claus plant
loadings with hydrogen sulphide and ammonia are increasing and the Claus plant may become a
bottleneck.
The problem can be overcome by oxygen enrichment of the combustion air. This increases the capacity
significantly. A new type of burner ensures excellent mixing of hydrogen sulphide and oxygen enriched air
over a wide load range.
Benefits of oxygen enrichment in Claus plants:
● Increased Claus plant capacity
● Increased productivity without changing the pressure drop
● More effective treatment of ammonia containing feeds
● Less effort for tail gas purification (reduced nitrogen flow).
Fluid catalytic cracking (FCC) converts primarily vacuum gas oil from the crude distillation unit into
gasoline blending stocks and fuel oils. FCC breaks down heavier and more complex hydrocarbons into lighter
ones. Feed is primarily vacuum gas oil, often mixed with refinery residues. The main products are gas
fraction (mainly C3/C4), liquid fraction and coke (solid formation on the catalyst).
FCC oxygen enrichment involves the addition of a controlled flow of gaseous oxygen into the combustion
air.
The additional oxygen in the regenerator results in higher plant efficiency due to:
● Increased plant capacity by up to 35%
● More flexibility in the selection of feedstock, especially to enable use of heavier feedstock with a
higher
tendency to form coke
● Increased conversion ratio and gasoline yield
● Resolved air blower constraints
● Reduced CO in the regenerator off-gas
● Less abrasion of the catalyst and less erosion of the cyclones due to reduced gas velocity,
resulting in
less downtimes and repairs
In order to help control particulates, sulfur dioxide and NOx emissions from the FCC we offer the LOTOX®
technology. LOTOX® is a patented innovation that uses ozone to selectively oxidize insoluble NOx to highly
soluble species that can be easily removed in a wet scrubber. The benefits include increased capacity,
greater flexibility in the choice of feeds, increased conversion rates and reduced emissions.
Partial oxidation plants are used to form hydrogen, carbon monoxide, carbon dioxide and water from the
residues (liquids, highly viscous hydrocarbons) of the refining process.
The products can be used as synthesis gas, fuel gas or feed for hydrogen recovery. With tailored oxygen
supply for Partial Oxidation (POX) we can offer you the following benefits:
● Cleaner and better reuse of residues
● Broader economic base of the refinery
● Higher flexibility through a wider range of products
● Handling of refinery feed compositions within a wide range
We offer a vast service portfolio dedicated specifically to the needs of refinery operations. Pressure,
temperature, purity and volume requirements can vary significantly across a range of highly specialised
applications.
Many refinery operators rely on our nitrogen services – sometimes in combination with other gases – to
support the following applications:
● Drying and purging: Humidity in pipelines can delay start-up or compromise productivity for days. Purging
with large streams of gaseous nitrogen enables pipelines to be dried and heated in a controlled manner, thus
accelerating start-up and boosting productivity. We can supply nitrogen at flow rates of up to 25,000 m3/h
and at a pressure of up to 700 bar for these applications.
● Inerting and blanketing: We supply inert gases such as nitrogen or carbon dioxide (CO2) to bring oxygen
concentrations down to a safe level in environments with the potential for fire and explosions.
● Pipeline pigging: A pig is sometimes pressed through a duct or pipeline that requires cleaning or
inspection, especially if it contains viscous material. We supply gaseous nitrogen for this purpose. It is a
highly effective, safe and dry pressure medium, supporting a wide range of pressures, temperatures and
volume flow rates.
● Leak and pressure testing: We supply a special nitrogen/helium mixture to detect even tiny leaks and leakage
rates at operating conditions with pressures of up to 250 bar. The helium acts as an easily detectable
tracer gas as it is inert and diffusible. This is an effective, economical solution that enables operators
to rapidly remedy defects. We also supply high-pressure nitrogen for testing at pressures of up to 700 bar.
● Reactor cool-down with hot stripping: With our hot stripping and CATCOOL™ processes, refineries can shorten
by days the window needed to cool down high-temperature facilities in preparation for inspection. This inert
process technology relies on controlled streams of large volumes of cold nitrogen to reduce production
downtime.
● Pipe and ground freezing: Cryogenic nitrogen can be used to temporarily seal and freeze pipe sections for
installation or repair work. This smart solution eliminates the need to drain and shut down the entire
piping system. This method can also be used to freeze the ground for construction work.
Buy products here
Downloads
Safety datasheets | Product datasheets & brochures |
---|---|